Enhancing Performance and Durability with Overmolding
In the world of manufacturing, durability and dependability are crucial, especially in cable assemblies and wire harnesses. These components serve as the backbone of electrical and electronic systems, ensuring seamless power and data transmission. Overmolding has emerged as a leading method to enhance performance, reliability, and longevity by encasing these assemblies in protective polymers. In this article, we will explore why overmolding works so effectively in cable assembly and wire harness applications, with a focus on low-pressure molding (LPM).
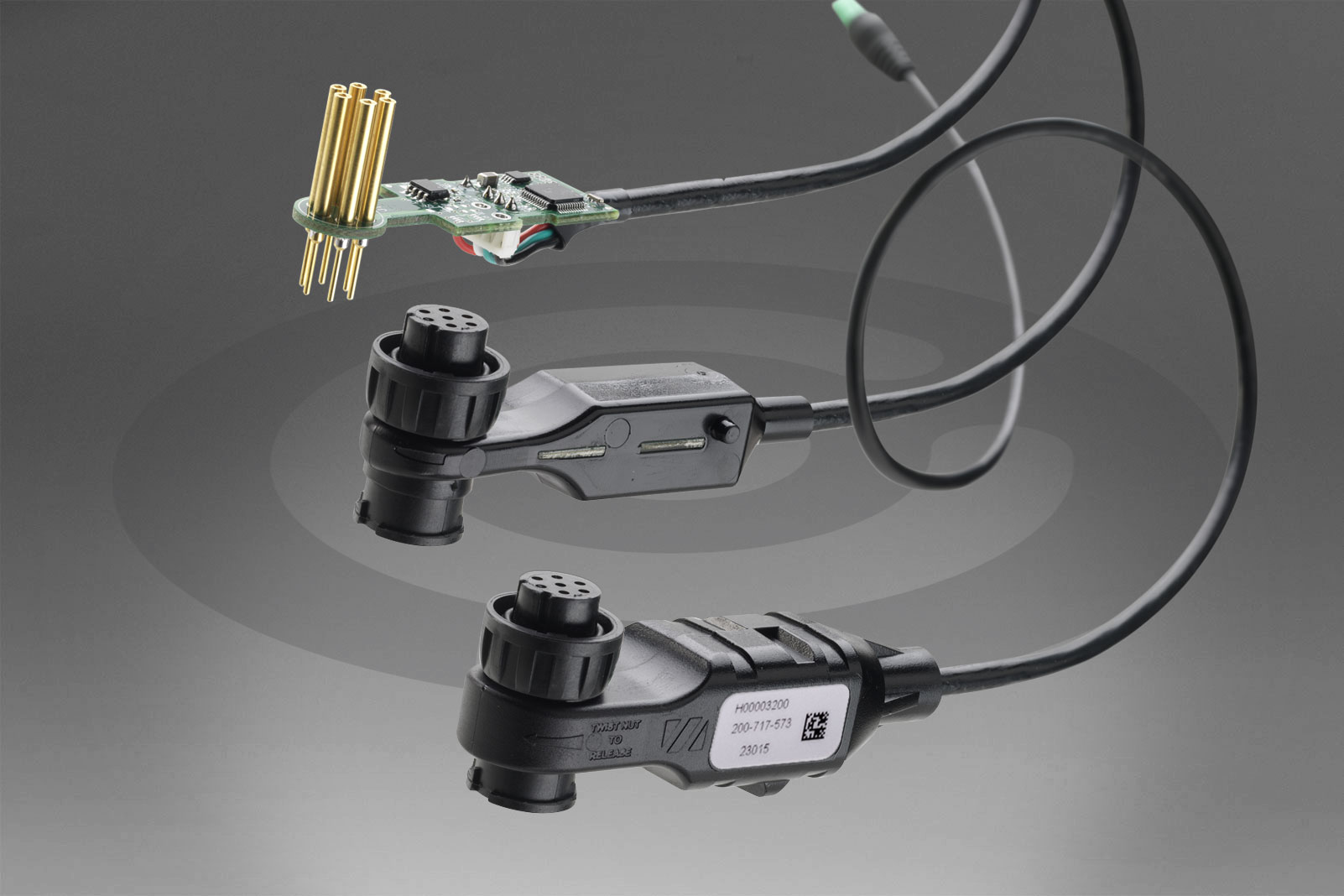
What is Overmolding?
Overmolding is a manufacturing technique in which a thermoplastic or thermoset material is molded over a substrate, such as a cable or wire harness. Low-pressure molding (LPM) is a specialized variation of this process, utilizing hot-melted polyamide injected under low pressure to minimize damage to sensitive components. This method provides a seamless protective layer, shielding the assembly from mechanical, electrical, and environmental stressors.
Key Benefits of Overmolding in Cable Assemblies and
Wire Harnesses
1. Superior Durability and Protection
Overmolding enhances the resilience of cable assemblies by offering protection against:
- Abrasion: Prevents wear and tear from friction.
- Impact: Absorbs shocks and vibrations, reducing internal damage.
- Moisture and Corrosion: Forms a hermetic seal to guard against harsh environmental conditions, ensuring long-term reliability.
This process is particularly effective in safeguarding delicate electronic components such as:
- Sensors
- Printed Circuit Boards (PCBs)
- Connectors and Terminals
2. Strain Relief and Mechanical Integrity
Overmolding reinforces critical connection points, relieving strain and increasing mechanical strength. This is especially important in dynamic environments such as industrial and automotive applications. By incorporating flexible bends or reinforced collars, overmolding distributes stress away from vital connection areas, reducing wear and tear and extending product lifespan.
3. Streamlined Production and Cost Efficiency
Compared to traditional sealing techniques, low-pressure overmolding simplifies production by eliminating secondary sealing steps. This reduces manufacturing time and cost while increasing production efficiency.
4. Enhanced Pull Strength
Encasing cables and wire harnesses in an overmolded protective layer significantly improves pull strength, allowing them to endure greater tension without failure. This reinforcement is crucial for applications requiring frequent handling or movement.
5. Laser Marking Capabilities
The smooth, durable surface created by overmolding allows for laser marking, enabling clear and permanent identification of part numbers, specifications, or branding. This ensures that critical information remains visible even in harsh environments.
Cavist Manufacturing: Your Overmolding Expert
Low-pressure overmolding has proven to be a game-changer in the cable assembly and wire harness industry, offering a perfect blend of efficiency, precision, and durability. At Cavist Manufacturing, we are dedicated to providing cutting-edge overmolding solutions that ensure your products perform reliably, even under extreme conditions.
Adopt overmolding for your cable assemblies and wire harnesses today to enhance performance, durability, and cost-efficiency in every application.
Reach out to Cavist to get more information about overmolding and encapsulation.